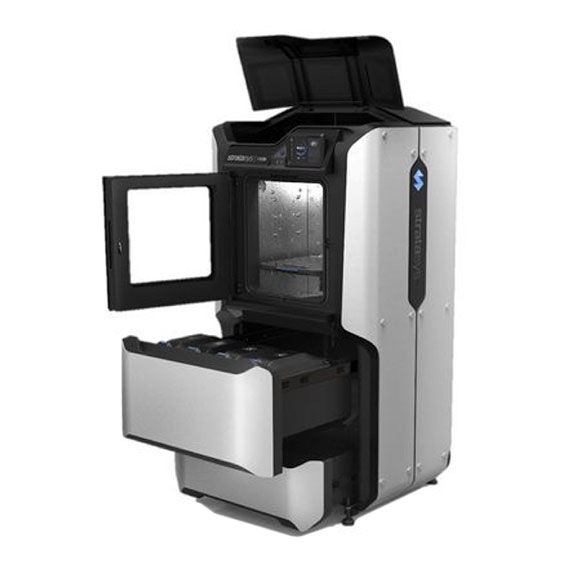
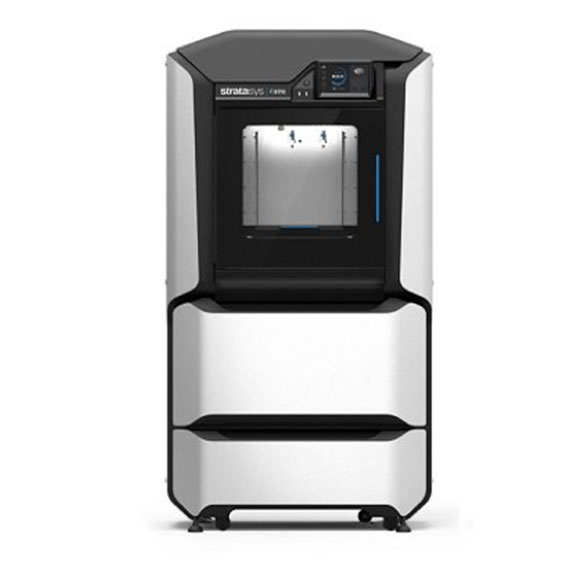
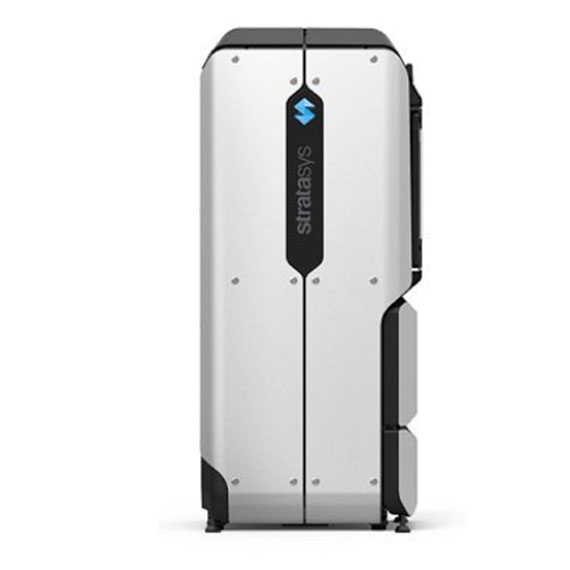
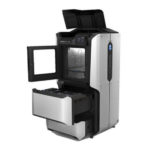
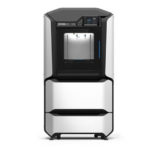
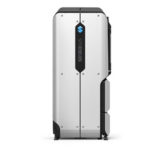
A Thermoformed Enclosure for a 3D Printer
CLIENT | Stratasys |
---|---|
MATERIAL | Kydex® T – Color Matched PVC Acrylic |
PROCESS | Pressure Forming |
INDUSTRY | 3D Printing |
Project Summary
Why would a 3D printer manufacturer choose pressure forming for their equipment enclosures? Because, after exploring all their options, pressure forming was the best process for their needs. Stratasys needed an attractive, durable and cost-effective enclosure for their brand-new F370 industrial-grade 3D printer.
After initially planning on a reaction injection-molded (RIM) enclosure, they came to understand the quality, aesthetic and capacity advantages that pressure forming can provide. We worked with them to shift the design to a 100% molded-in-color pressure-formed parts that not only met the project’s objectives perfectly, but also won a gold award in the SPE Thermoforming Division Parts Competition.
Project Details
Stratasys is often described as the world’s leading 3D printing company, and they’ve been at the forefront of 3D printing for over 30 years. That’s why we were thrilled when they approached us about making the enclosure for their brand-new F370 industrial 3D printer.
Originally, the enclosure was slated to be made using reaction injection molding (RIM), but as the company’s engineers and designers researched manufacturing processes, they came across some of the key benefits of pressure forming that made it a better option for their project — namely, the ability to mold in color, larger-part capabilities, molded-in attachment features and improved manufacturing speed.
In working with Stratasys, we were able to reduce the total number of parts required, as well as eliminate structural ribs from the design owing to the strength of the pressure-formed part. By molding in color, we were able to eliminate painting from the final process and reduce costs while increasing manufacturing speed.
Additionally, pressure forming allowed for the addition of molded-in features and undercuts that nearly eliminated the need for bonded attachment points.
That’s not to say that the project wasn’t without its challenges. The design called for two undercuts that were incorporated into the drawers at the front of the unit, one with a depth of 2.5”. In fact, when we sent the design to our toolmaker, he voiced concerns that what we were trying to do might not be possible.
In the end, by working closely with Stratasys, our toolmaker and our skilled internal production team, we were able to successfully manufacture the undercuts and create a truly unique pressure-formed part in the process. Thanks to the close collaboration, the components were manufactured quickly, allowing Stratasys to get a jump on bringing their product to market in a rapidly evolving competitive landscape.
Today, the F370 printers are a leading option in the marketplace, and are being used for prototyping and production in the aerospace, automotive, consumer products and medical spaces. We were also excited enough about the enclosure to submit it as our entry for the 2019 Society of Plastic Engineers (SPE) Thermoforming Division Parts Competition. We were thrilled to have it win gold.