Know The Difference
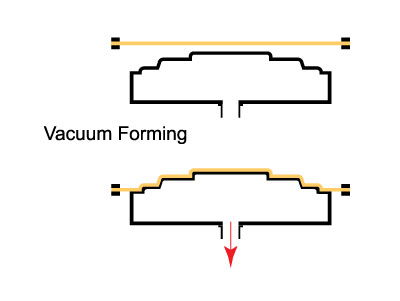
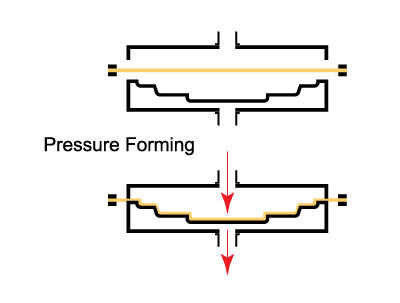
VACUUM FORMING | PRESSURE FORMING | |
---|---|---|
DESCRIPTION | A sheet of plastic material is heated to pliability, then pressed against a 3D mold by vacuuming out the air between the sheet, and the mold. | A sheet of plastic material is heated to pliability, then pressed against a 3D mold by vacuuming out the air between the sheet and the mold, and applying air pressure above the plastic sheet. |
KEY ADVANTAGES |
|
|
PERFECT FOR |
|
|
OFTEN USED TO CREATE |
|
|
Pressure Formed Projects
Vacuum Formed Projects