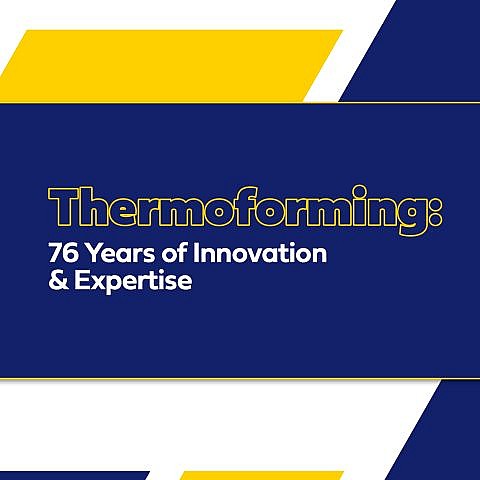
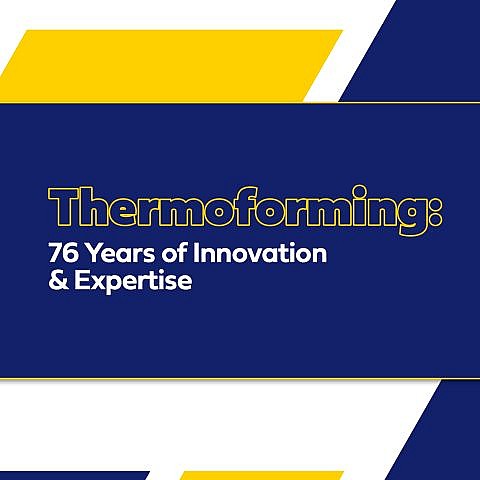
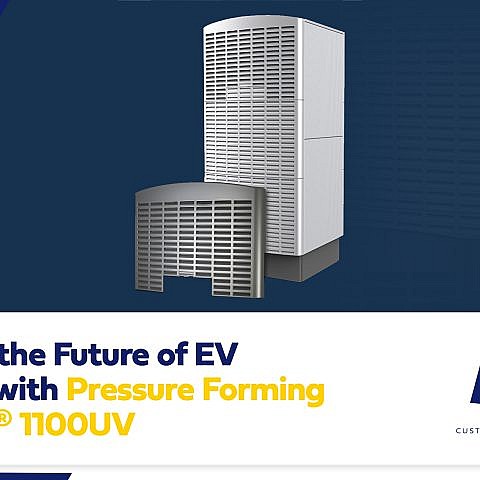
Case Study: Ray Products and SEKISUI KYDEX Collaboration
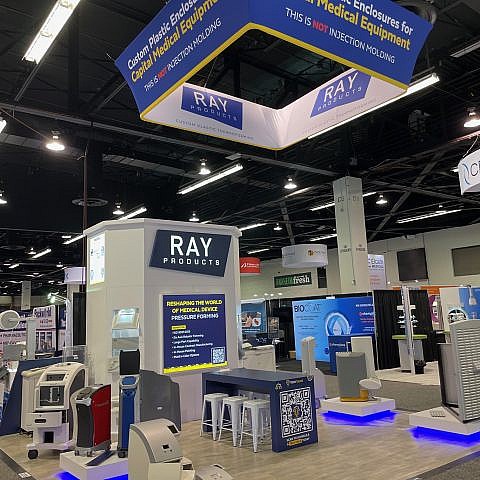
MD&M West 2025 Trends: Innovations Shaping Medical Manufacturing
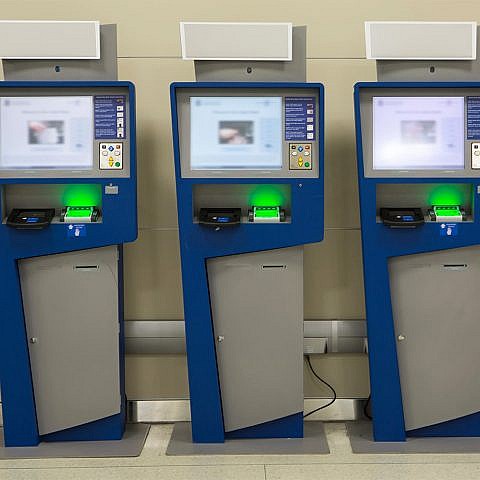
Thermoforming: The Future of Kiosk and POS Design
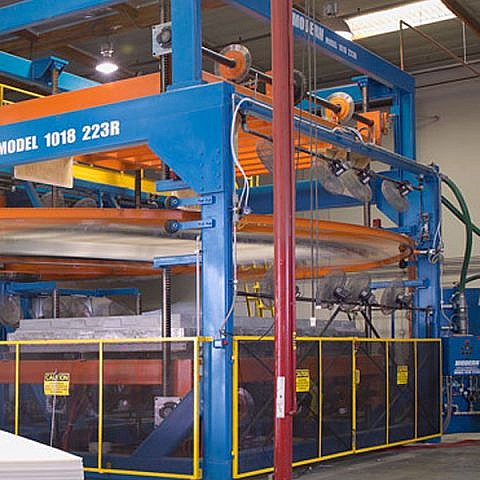
The Future of Thermoforming: Trends and Innovations to Watch

Insights from the 2023 SPE Thermoforming Conference
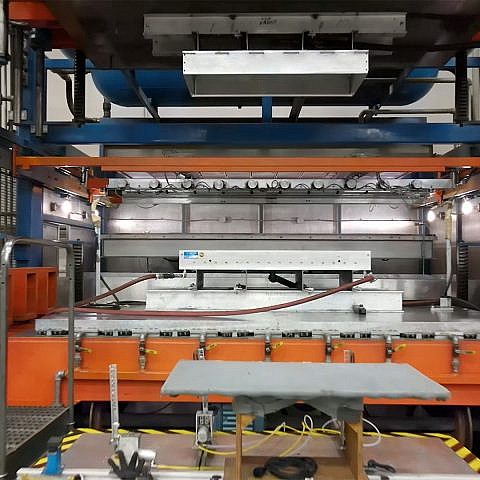
The Ins and Outs of Pressure Forming
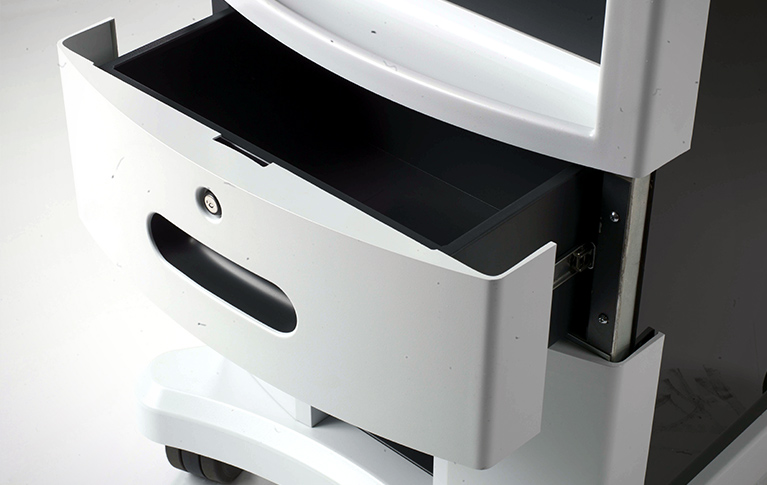
3 Ways Large Part Thermoforming Redefines What’s Possible
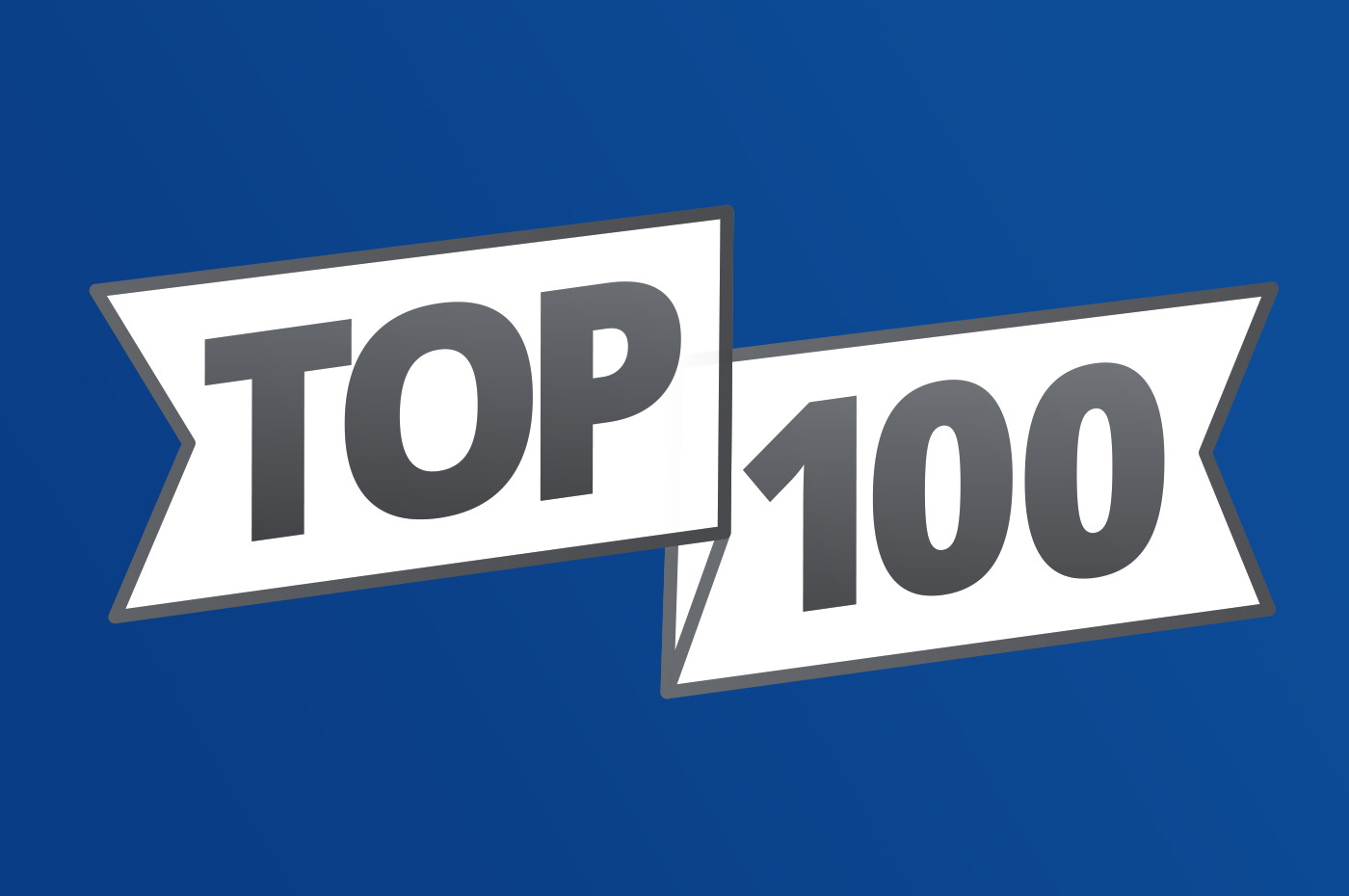