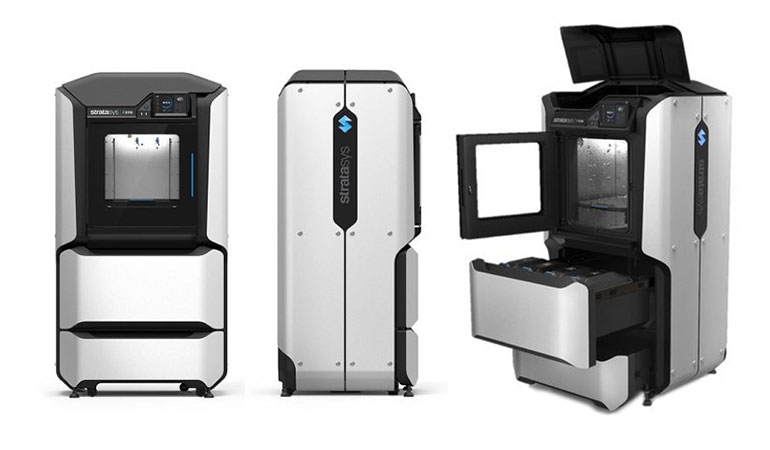
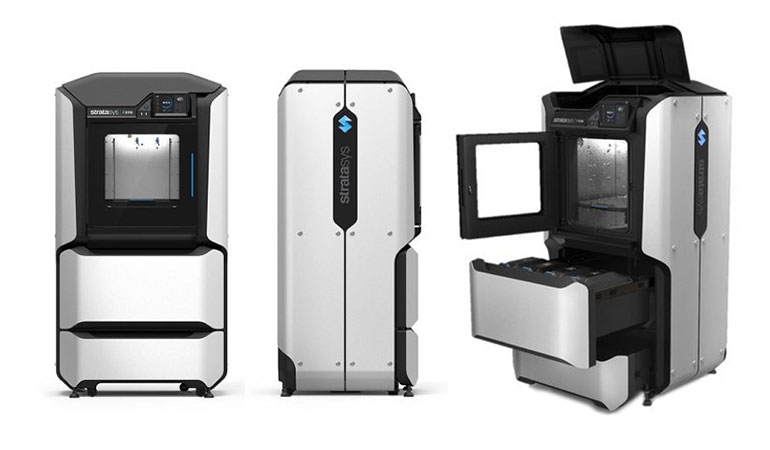
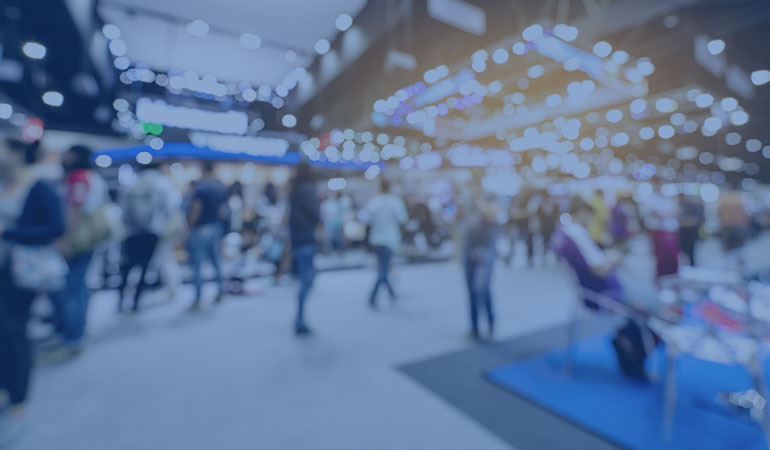
Upcoming Thermoforming and Manufacturing Tradeshows
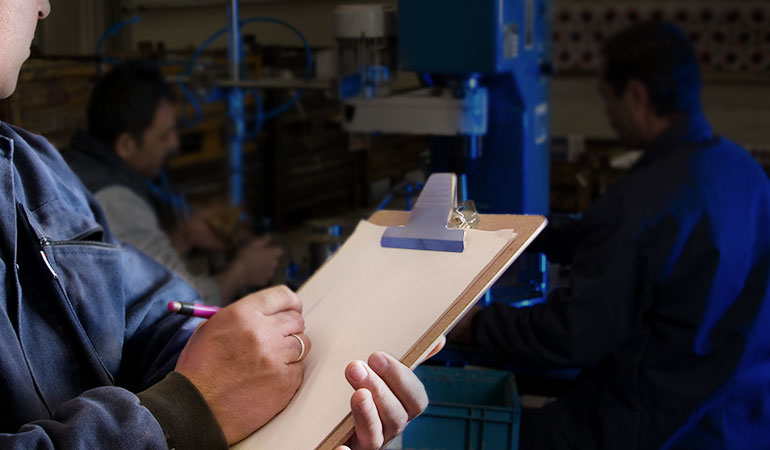
Lessons from a PhD-Grade Industrial Energy Audit
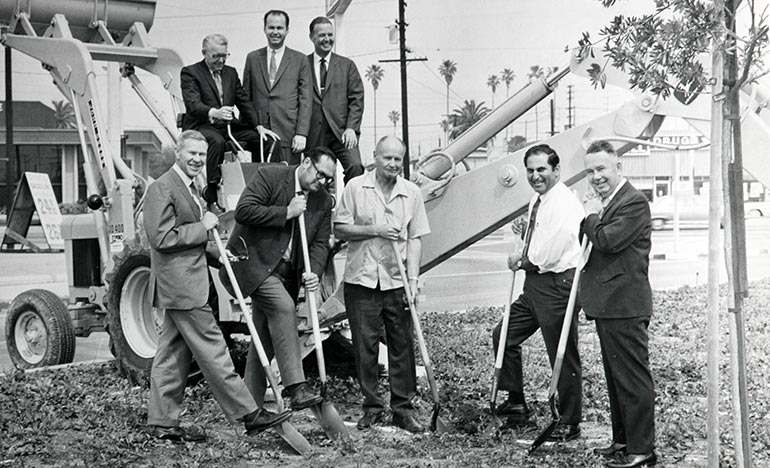
Ontario Plastics Manufacturer Celebrates 70 Years
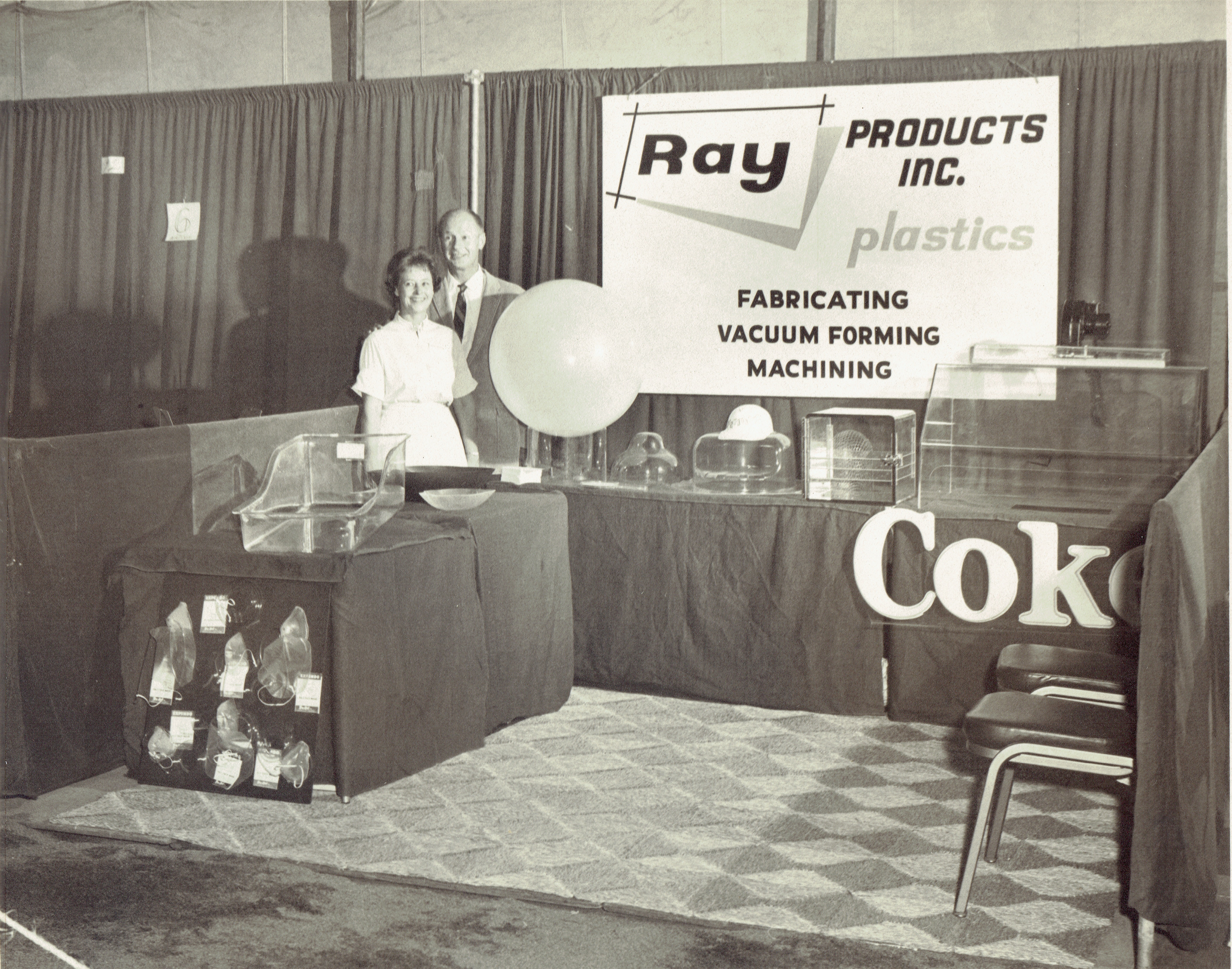
A Story 70 Years in the Making
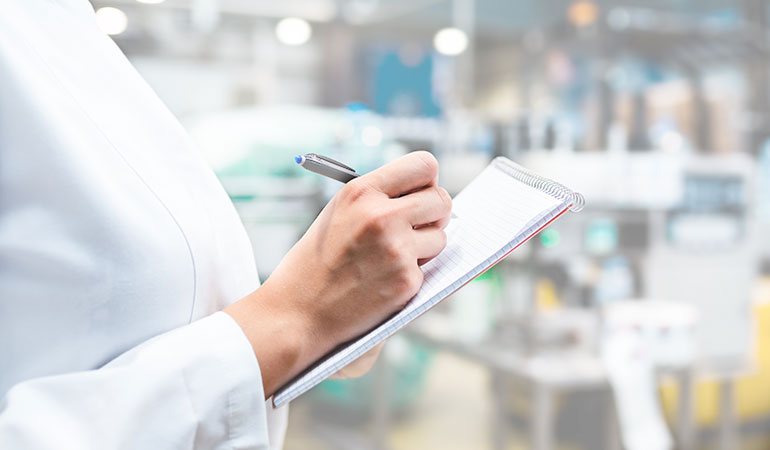
Thermoforming Precision & Quality, ISO 9001 Certification

A 50-Year Milestone
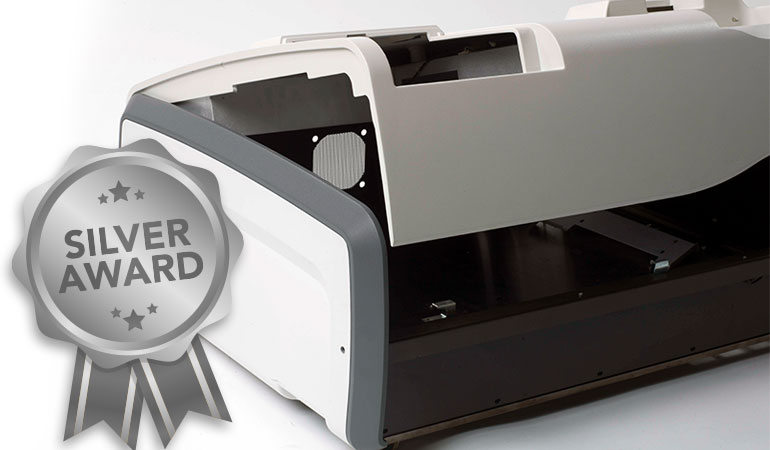
Awarded Silver at Plastics Engineers’ Thermoforming Conference
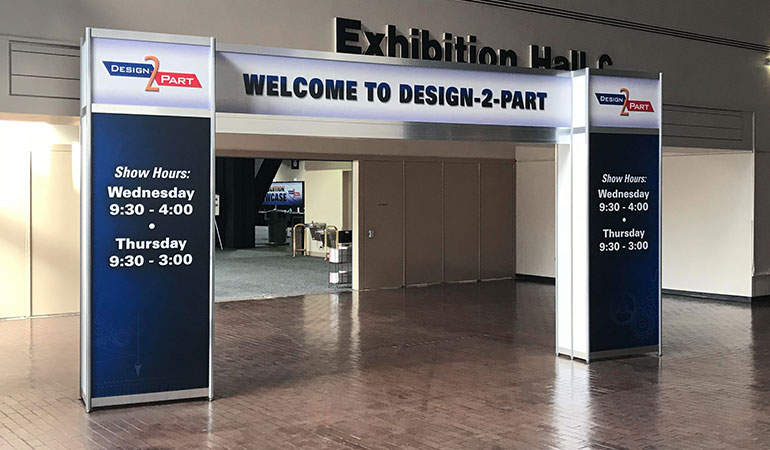