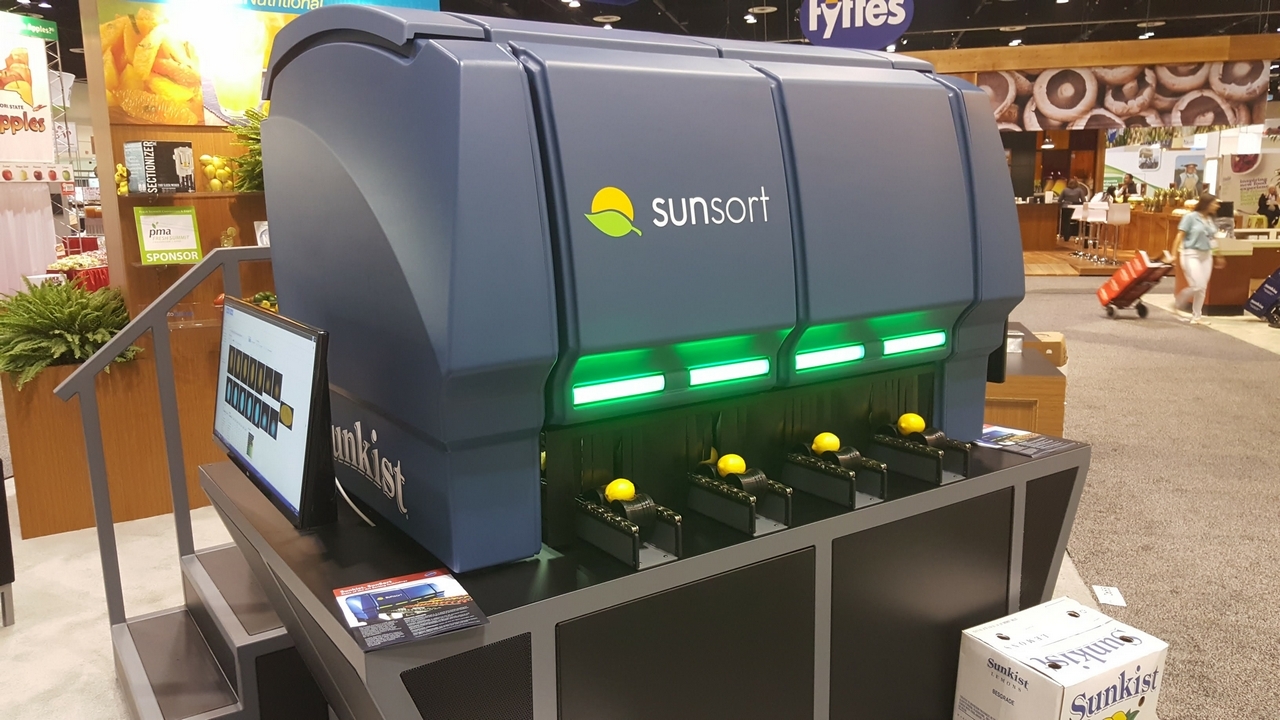
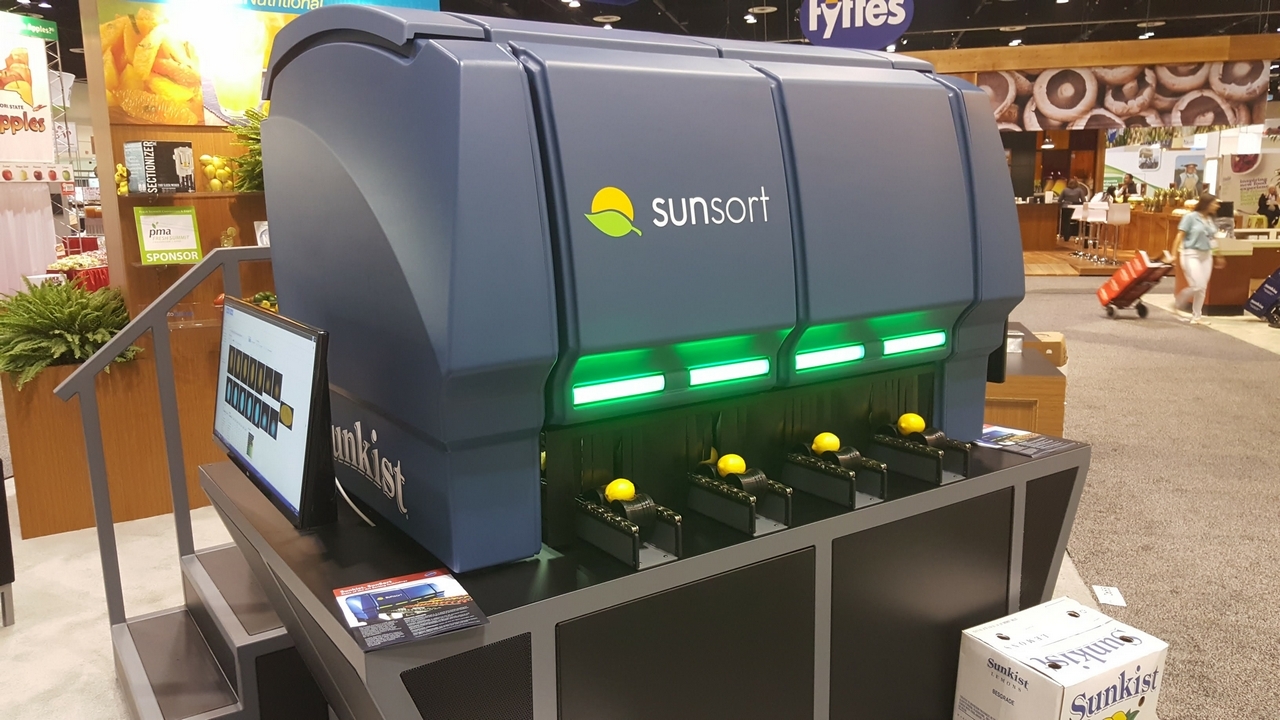

If Ray Products Were a Country, We’d Be the Most Advanced Country
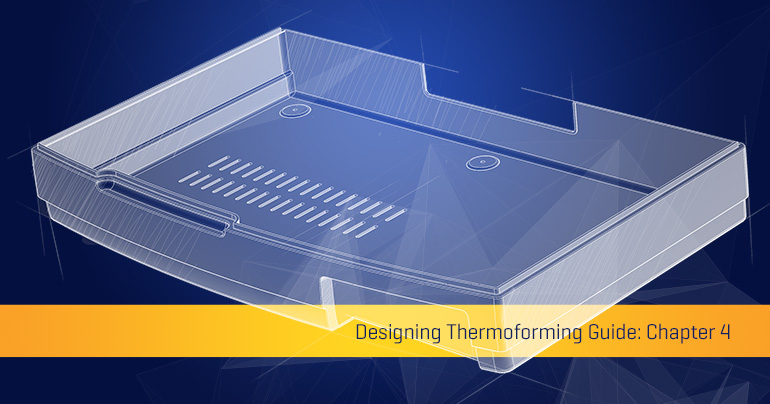
Thermoforming Materials Selection: From the Design Guide Chapter 4
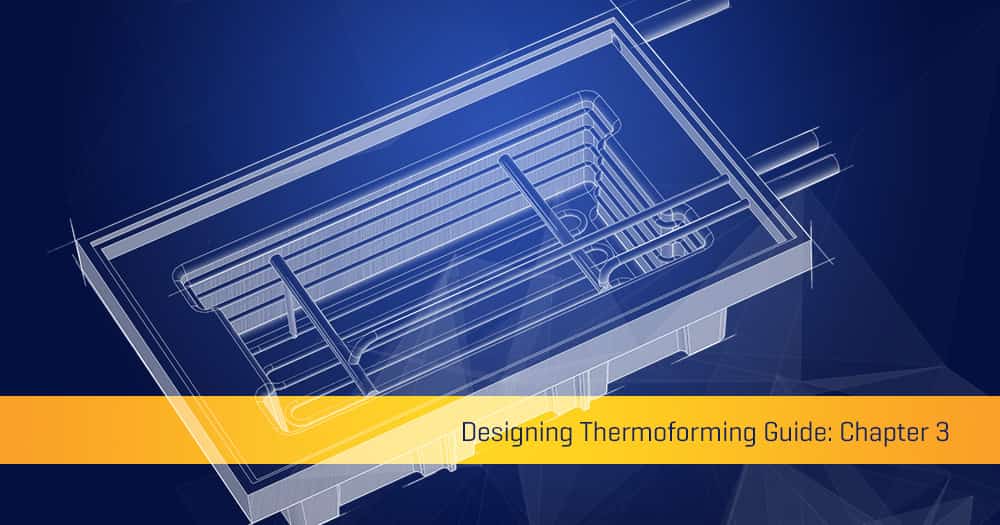
Tooling, The Foundation of Thermoforming: From the Design Guide Chapter 3
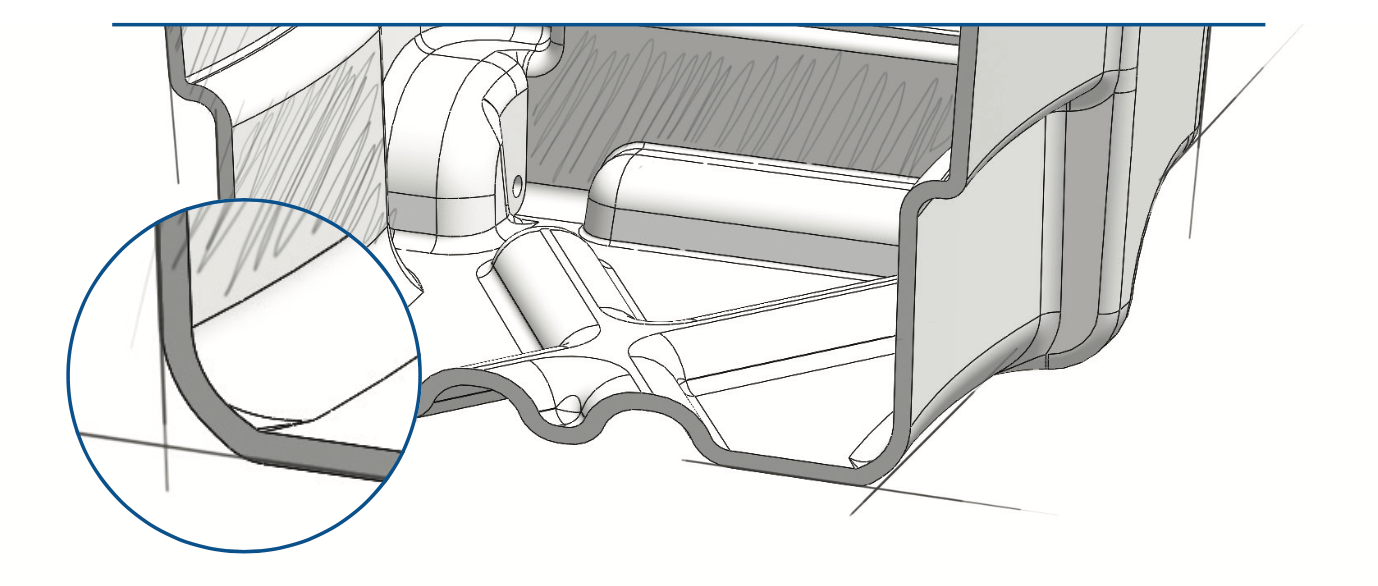
Designing for Thermoforming: From the Design Guide — Chapter 2
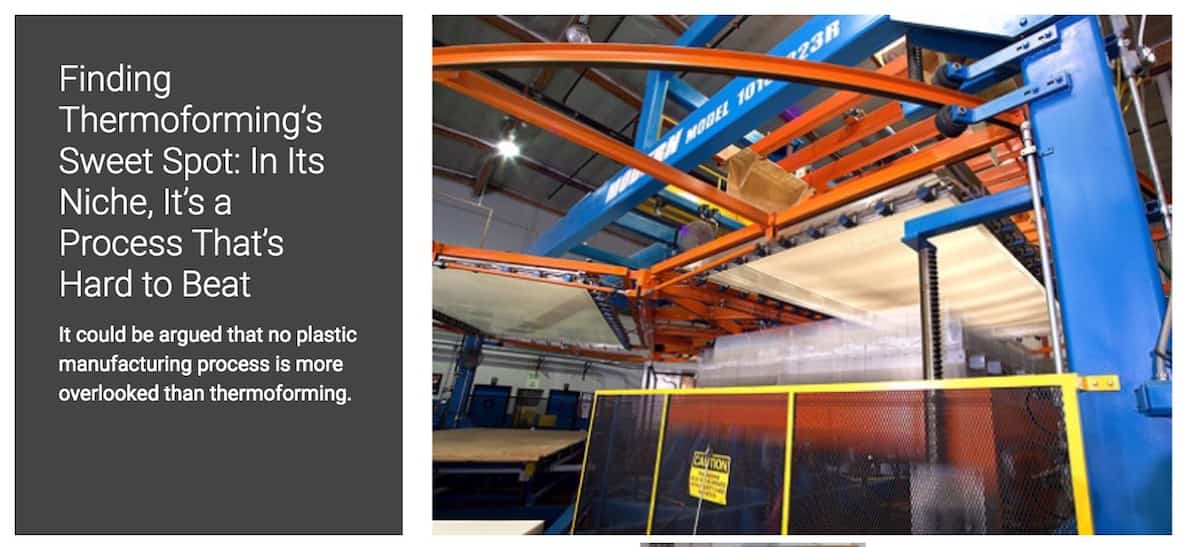
Finding Thermoforming’s Sweet Spot in MFR Tech
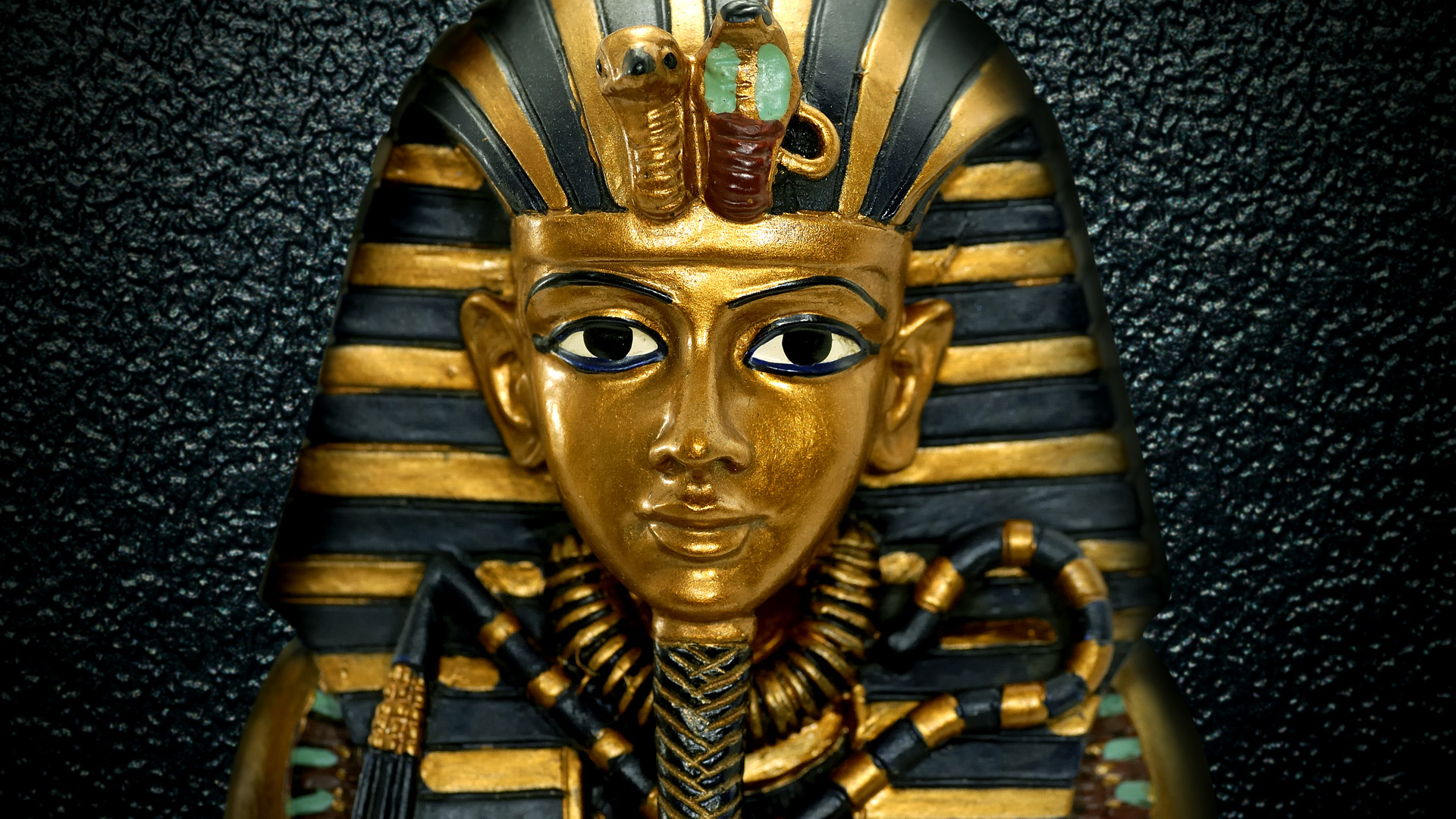
Thermoforming, Ancient Egyptians and 3D Printing
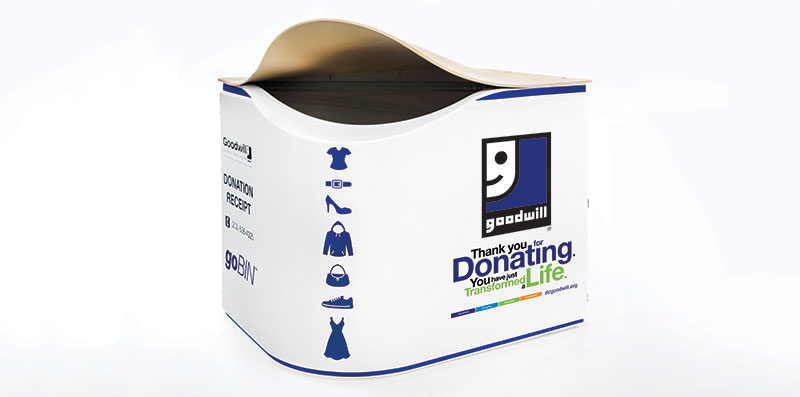
Helping Goodwill Save Money and Improve their Donation Bins
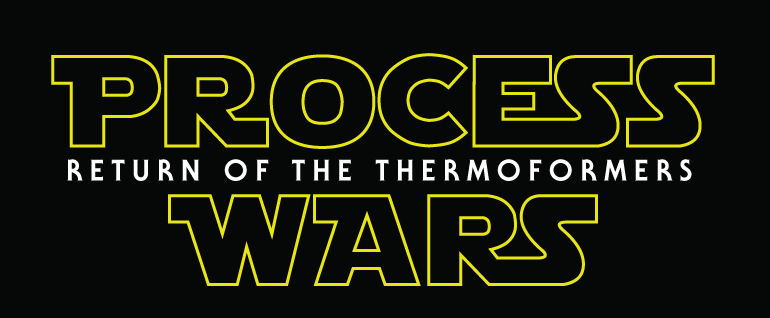